TA15-BT20

TA15-BT20 variety introduction
The nominal composition of TA15 Titanium alloy is Ti-6.5Al-2Zr-1Mo-1V. The main reinforcement mechanism is solid solution reinforcement by α-stable element Al. The addition of neutral elements Zr and β stable elements Mo and V can improve the processability.The alloy has an Al equivalent of 6.58% and Mo equivalent of 2.46%, which is a near α type Titanium alloy with high Al equivalent. Therefore, it not only has the good thermal strength and weldability of α Titanium alloy, but also has the α process plasticity close to β Titanium alloy.
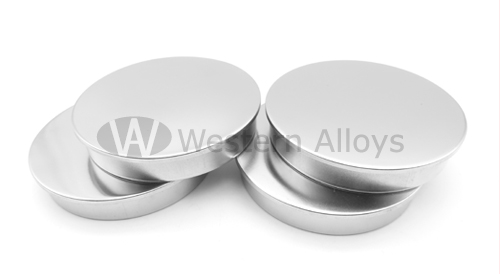
Semi-finished products of TA15 alloy include sheet, plate, rolled bar, forged bar, die forging, forgings, extruded profiles, welded rings, solid ring rolled parts and castings.
TA15-BT20 alloy chemical composition
|
TA15-BT20 alloy properties
|
TA15 Heat treatment system
1) Annealing
700-800℃, 15-60min, air-cooled; Bars, forgings, die forgings, thick-wall profiles and parts: 700-850°C, 1-4h, air-cooled.
2) Stress relief annealing
600-650℃, 0.5-8h, air-cooled.
TA15 welding performance
The alloy has good welding properties for argon arc welding, contact welding and submerged arc welding. The strength of the weld at room temperature and high temperature is 90%-95% of the strength of the base material.
The joint is not sensitive to heat treatment.
Heat treatment process of TA15 parts
TA15 smelting casting process
The alloy should be melted three times in a vacuum consumable electrode arc furnace. Castings are poured in a vacuum consumable arc condensing furnace.TA15 Use recommendations
TA15 Titanium alloys are recommended for various load-bearing components on aircraft and engines.TA15 Application overview and special requirements
Effect of heat treatment on mechanicl properties of TA15 titanium alloy bars:(a) single heat treatment;(b)dual heat treatment